A frugal CNC Oxyfuel Cutter
An open source CNC gas cutter for resource constrained settings
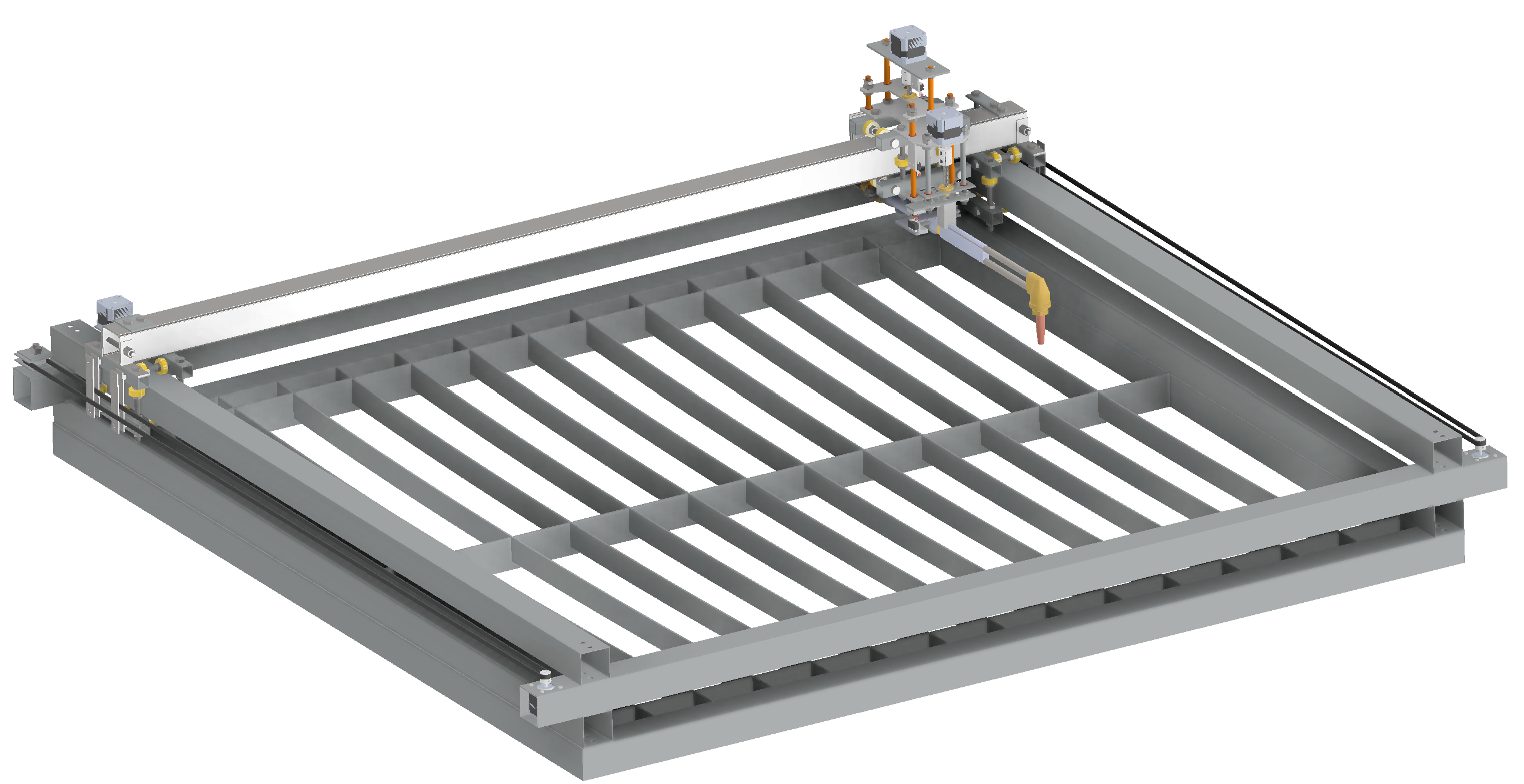
Project Overview
This project presents a low-cost CNC oxyfuel cutter designed specifically for metal fabrication microenterprises in Oman. These small workshops often build structural and non-structural items such as gates, staircases, warehouses, and furniture — all requiring the cutting of thick steel plates (3–50+ mm).
Despite the efficiency of automated cutting, CNC machines remain inaccessible to these workshops due to high cost, limited space, and lack of local availability.
Understanding User Needs
A field study was conducted in the industrial cluster of Wadi Kabir Sanaya, Muscat. Most workshops are open-air, compact (15–20 m²), and operated by 2–3 migrant workers from South Asia. Key insights from interviews and observations include:
- No existing use of CNC or digital fabrication tools
- Frequent use of handheld oxyfuel torches
- Cutting done on full or scrap sheets, often outside due to their weight
- Strong preference for compact, affordable, and stowable machines
- Limited access to electronics or precision components locally
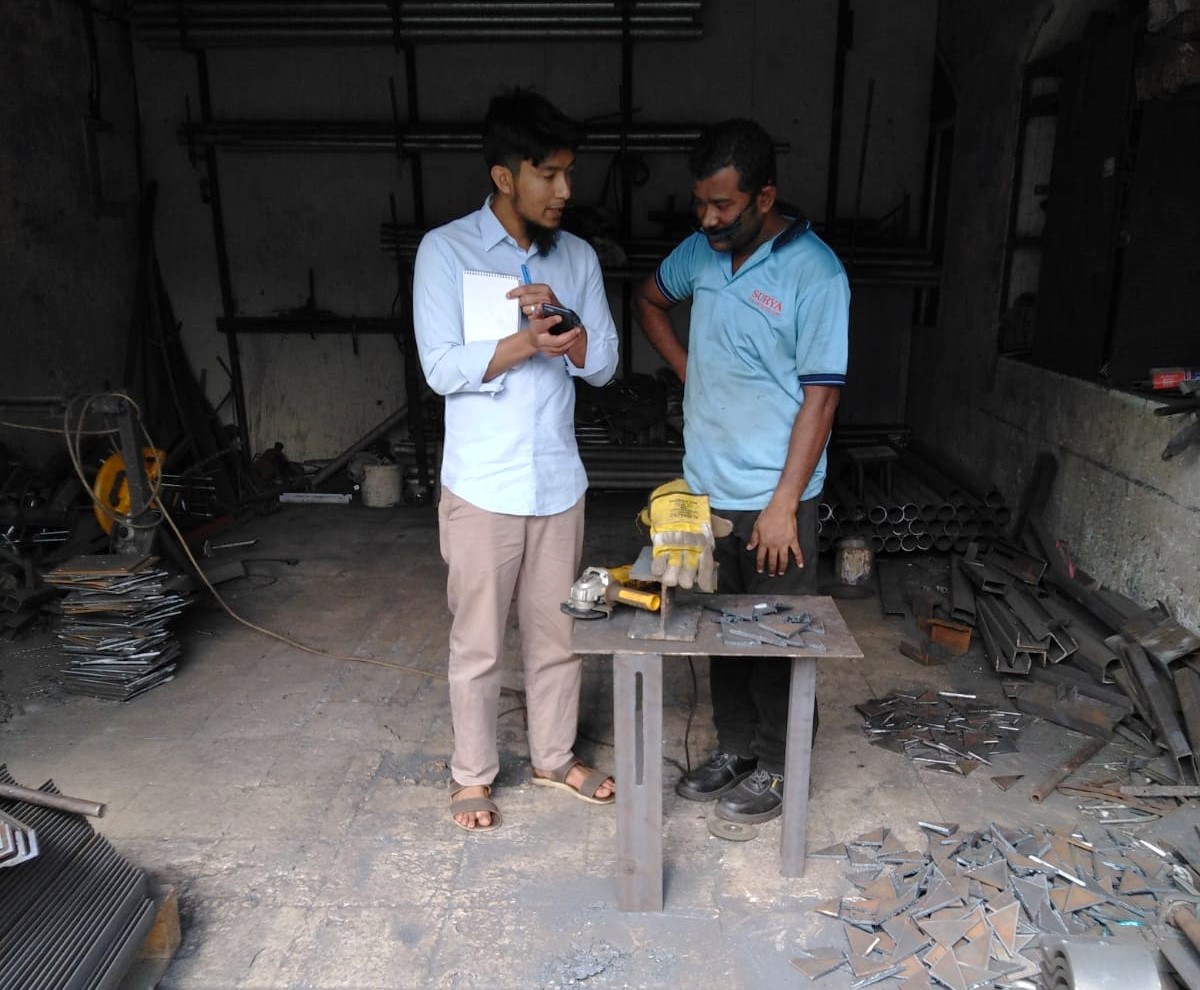
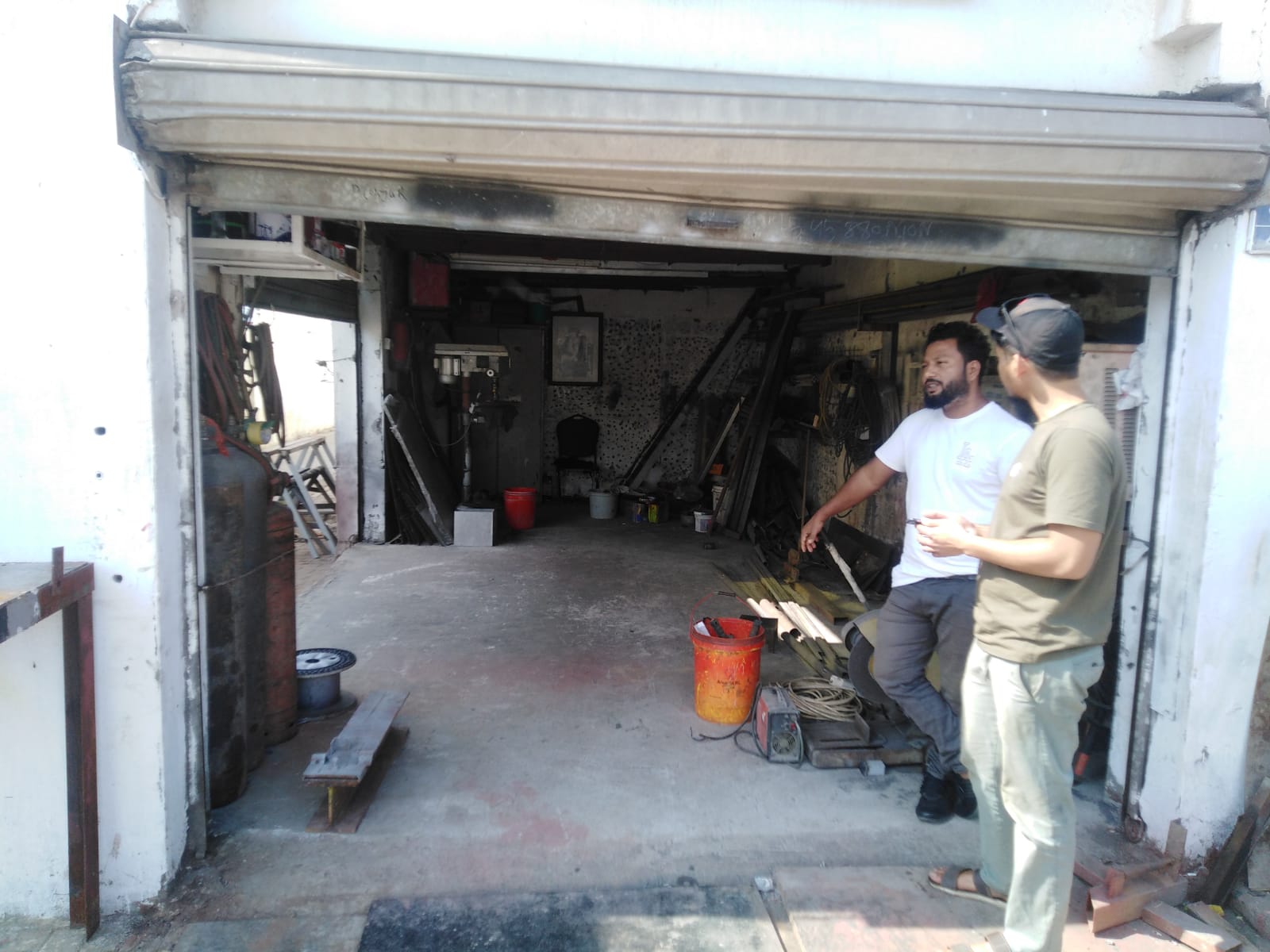
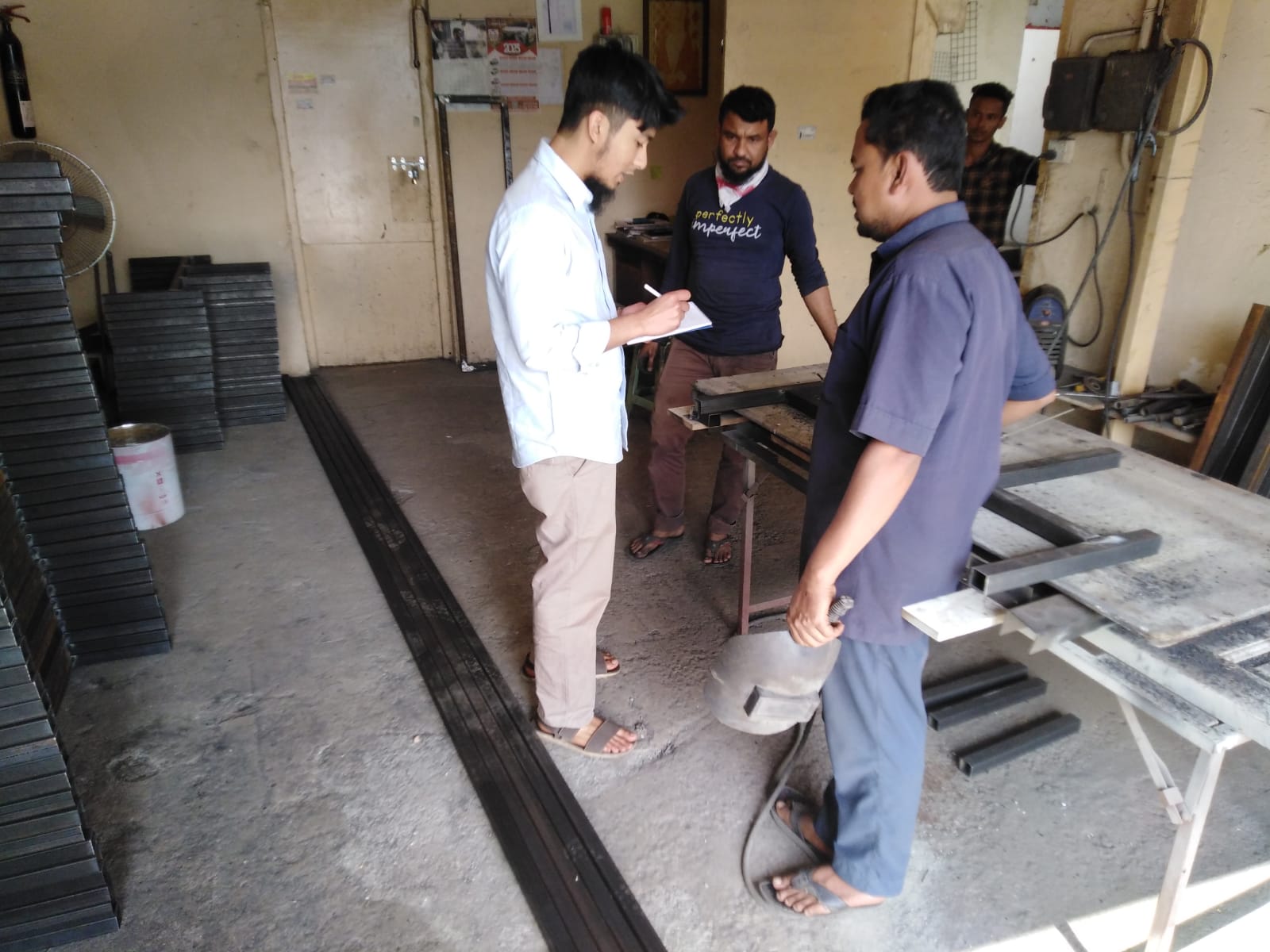
Design Decisions
Why Oxyfuel Cutting?
Among various fabrication processes, gas cutting was selected for automation due to:
- High repetition of cutting tasks
- Time-consuming and hazardous manual cutting
- Poor cut quality requiring extensive post-processing
Frugal, Participatory Design
The machine was designed with end users using a co-design approach whereby the prototype was fabricated within one of the workshops. Workers participated in:
- Suggesting fabrication methods
- Design improvements
- Solving design challenges during assembly for example by co-designing by prptotyping some of the complex sub-assemblies like the Z-axis
- Assembling the machine frame in the workshop
Local Constraints and Adaptations
- The machine was built from easily available surplus workshop materials (e.g., 2” square steel tubing)
- Simple linear guides using locally available roller bearings
- No reliance on imported machine torches — compatible with users’ own handheld torches
- Fabrication aided by paper templates for marking and drillingpp
// put picture of the excel sheet of available local material, next to it show the basic hand torch
- Materials like aluminum and precision linear rails were unavailable or too expensive
- No access to standard machine parts (e.g., M3 screws), so designs were adapted
- CAD development followed field sketches and rough calculations
//put picture of the workshop setting, and a drilling picture to show jibg
Key Features
- Affordable: Target price $500–800 (small shops), up to $3000 (larger shops)
- Compact: Easily stowable when not in use
- Safe & Efficient: Reduces risk, labor, and post-processing
- User-Centric: Designed and built with the microenterprise workers taking local materials and capabilities into account
Prototyping
Gallery
References
2023
- Exploring the Potential of Open Source Machine Tools for Sustainable Industrial Development in Low Resource Contexts - A Case Study of Migrant-Run Microenterprises in OmanIn Manufacturing Driving Circular Economy, 2023
2022
- Democratizing Manufacturing – Conceptualizing the Potential of Open Source Machine Tools as Drivers of Sustainable Industrial Development in Resource Constrained Contexts2022